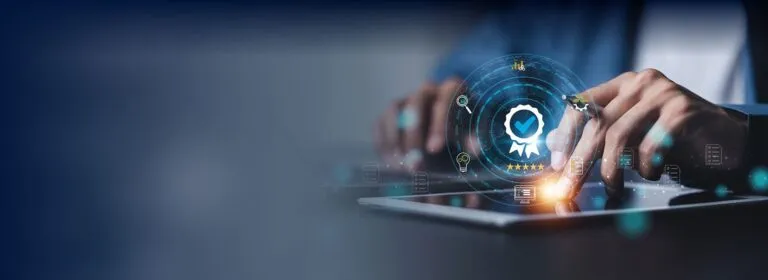
Quality
Trinzo is committed to providing solutions that support the ability of life science companies to deliver innovative solutions that improve patient healthcare.
Observing the highest standards of quality within the life sciences industry, we support our clients across a range of services that include Quality System Development, Quality Assurance, Audits (internal, mock, FDA, MDR, IVDR) and much more.
Quality System Development and Enhancement
We know that a robust Quality Management System (QMS) is the backbone of compliance and operational excellence. Our support in Quality System Development and Enhancement is steeped in experience across Quality System Regulations (QSR), cGMP, ISO 13485, EU MDR, IVDR, and MDSAP frameworks. Whether you’re refining an existing system or building a QMS from the ground up, our team collaborates closely with yours to design a system that is both resilient and adaptable to industry changes. For organizations undergoing mergers and acquisitions, we conduct thorough quality system assessments, manage seamless integrations, and ensure that your newly merged organization operates with a unified, compliant QMS. With Trinzo, project management is a given—our experts are adept at steering QMS projects to completion on time, in budget and within scope, giving leaders a streamlined experience and a compliant result.
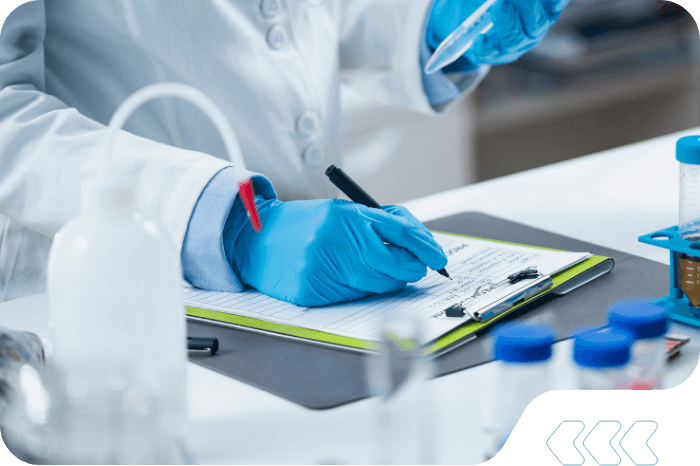
Quality Assurance
Maintaining consistent quality across the lifecycle of a product requires a strategic and thorough approach to quality assurance. Our Quality Assurance services cover everything from Design Quality Assurance (DQA) and Supplier Quality Engineering (SQE) to comprehensive support for nonconformance management, CAPA, and Supplier Corrective Action Requests (SCAR). We know that for leaders mitigating risks from suppliers and throughout production is critical. With Trinzo’s quality engineering support, you gain a robust strategy against compliance risks that could impact production or patient safety. In the context of M&A, our team ensures that quality standards are consistent across both legacy and newly acquired entities, managing change and integrating best practices to strengthen quality at every stage.
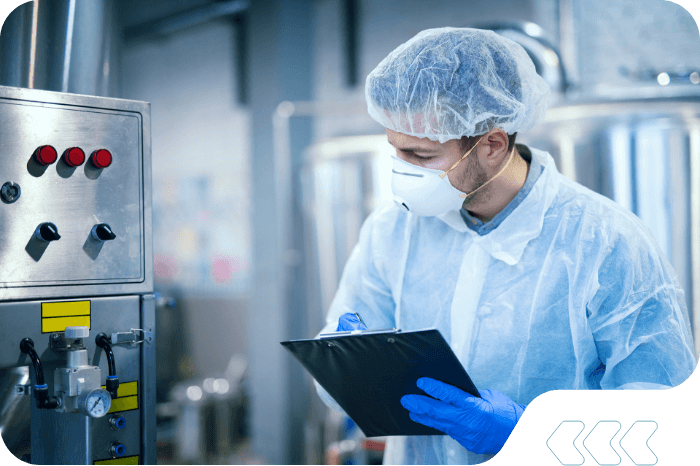
Audit and Inspection Management and Support
Regulatory inspections and audits are integral to the MedTech industry, but with the right preparation, they don’t need to be stressful. At Trinzo, we prepare clients to face regulatory scrutiny with confidence, offering services that include internal audits, mock inspections, QMS gap assessments, and supplier audits across MDSAP, ISO 13485, 21 CFR 820, GMP, and GDP. We recognize that, for leaders, the real value lies in creating a proactive audit-ready culture. That’s why we don’t just prepare for the next audit—we develop audit processes and provide readiness training that embed compliance into your everyday operations. During M&A activities, our audit and inspection management services bring both sides of the organization into alignment, identifying and remediating gaps and ensuring unified compliance post-acquisition.
- Internal Audits
- MDSAP Audit
- Mock FDA Inspection
- ISO 13485 Audit
- 21 CFR 820 Audit
- Good Manufacturing Practice (GMP) Audit
- Good Distribution Practice (GDP) Audit
- MDR QMS Audit
- IVDR QMS Audit
- QMS Gap Assessment
- Supplier Audits
- Audit/Inspection Readiness Training (Trinzo Training)
- Audit Remediation
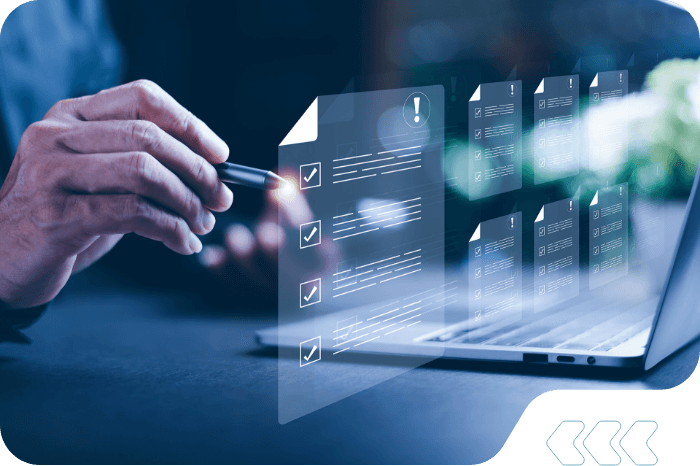
Manufacturing
Ensuring that manufacturing processes meet business needs and meet stringent regulatory standards is key to protecting product quality and patient safety. Trinzo’s manufacturing support encompasses technology transfer, process validation (IQ/OQ/PQ), computer system validation (CSV), and validation for capital equipment, packaging, and sterilization. Our hands-on, practical support ensures that each stage of manufacturing—from technology transfer and line setup to final validation—is compliant, controlled, and optimized. For organizations expanding through acquisitions, we also focus on aligning manufacturing practices across entities, supporting validation, and process stabilisation and standardization to enable a seamless transition and reliable, compliant output. With project management at the core of our approach, we prioritize timelines and coordinate every element to deliver results that align with your strategic and regulatory goals.
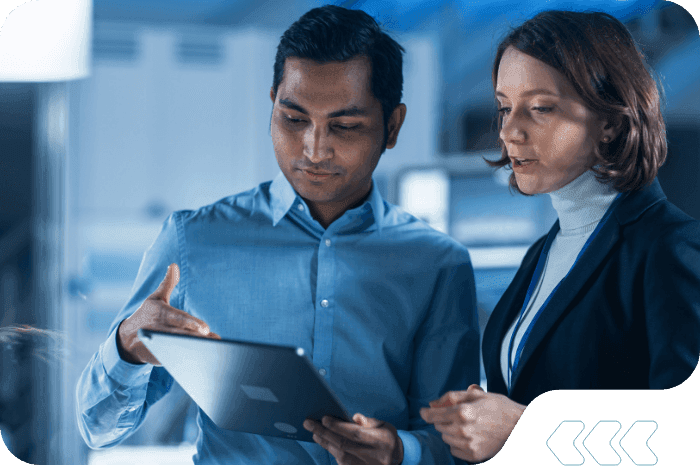
Risk Management
In a high-stakes environment, mitigating risk is paramount. Our Risk Management services, built on ISO 14971 standards, provide a systematic approach to identifying, assessing, and managing risks at every stage of the product lifecycle. From early risk assessments during design to comprehensive post-market monitoring, our team supports clients in establishing a risk management process that not only meets regulatory standards but also reinforces patient safety and brand reputation. In M&A scenarios, we integrate risk management practices to unify the risk culture across the organization, ensuring that product safety remains the priority.
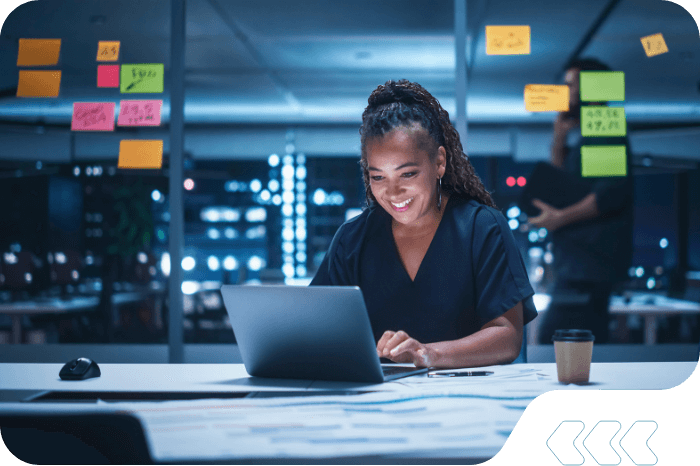
Lean Validation Support
Cost-effective validation processes to reduce waste and maintain high levels of quality control, compliance and product development.
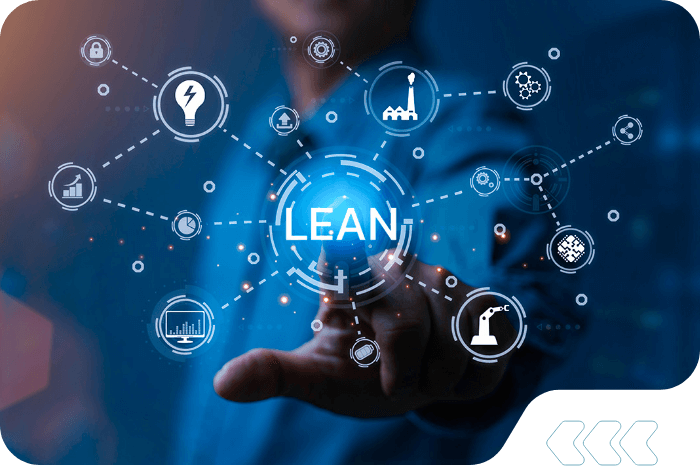
Our comprehensive audit services identify quality system deficiencies and ensure you are well-prepared for external audits when needed.
Support ranges from project-based solutions to broader strategic services, ensuring compliance with regulations and standards throughout your global quality processes.