Medical device remediation is a critical process that ensures compliance with regulatory requirements, maintains product safety, and minimises business risks. However, many companies make costly mistakes in the early stages of remediation, leading to delays, resource overextension, and compliance failures. These missteps often stem from a lack of strategic planning, misalignment of teams, and underestimation of the effort required.
A well-structured remediation approach is essential to navigating these challenges efficiently. By addressing key risks early, medical device organisations can avoid unnecessary setbacks and position themselves for long-term compliance success. This article highlights seven common early-stage mistakes in medical device remediation and how to prevent them.
1. Insufficient Understanding of Regulatory Scope
A critical first step in any remediation effort is understanding the full scope of regulatory requirements. Many companies fail to conduct a thorough review of their entire product portfolio, leading to compliance gaps that emerge later in the process. Regulatory requirements often evolve, and overlooking how they apply to both new and legacy products can result in incomplete remediation efforts.
To avoid this mistake, companies must invest in expert regulatory assessments to ensure all relevant requirements are considered. This includes reviewing FDA regulations, ISO standards, and any regional requirements applicable to international markets. A well-informed remediation approach ensures compliance is comprehensive, reducing the risk of future enforcement actions.
Check out our EU Medical Device Regulation Guidebook here. It provides you with an overview of the requirements of MDR so you can demonstrate compliance confidently.
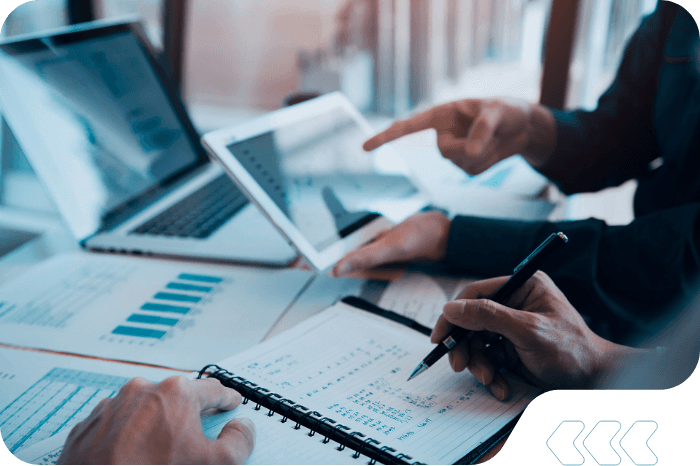
2. Lack of a Clear Remediation Strategy
Jumping into remediation without a well-defined strategy often leads to wasted resources, delays, and rework. Without clear goals, timelines, and a structured plan, efforts can quickly become disorganised, impacting both compliance outcomes and operational efficiency.
An effective approach starts with setting clear objectives, assigning roles, and establishing a timeline that aligns with regulatory deadlines. Cross-functional collaboration is essential, as remediation affects multiple departments, from quality and regulatory affairs to engineering and manufacturing. Companies should also establish a robust documentation process to track progress and demonstrate compliance to regulators.
3. Underestimating Cross-Functional Collaboration
Medical device remediation is not just a regulatory or quality issue—it impacts multiple areas of an organisation. When teams work in silos, inconsistencies in processes and documentation arise, creating inefficiencies and increasing the risk of noncompliance. A lack of collaboration slows down regulatory submissions, delays remediation progress, and makes it difficult to resolve quality management system (QMS) issues.
To mitigate this risk, companies should implement a structured communication framework that promotes alignment between departments. Regular cross-functional meetings, shared documentation platforms, and dedicated remediation task forces can help ensure all teams work toward a unified goal. An integrated approach enables smoother execution and reduces compliance risks.
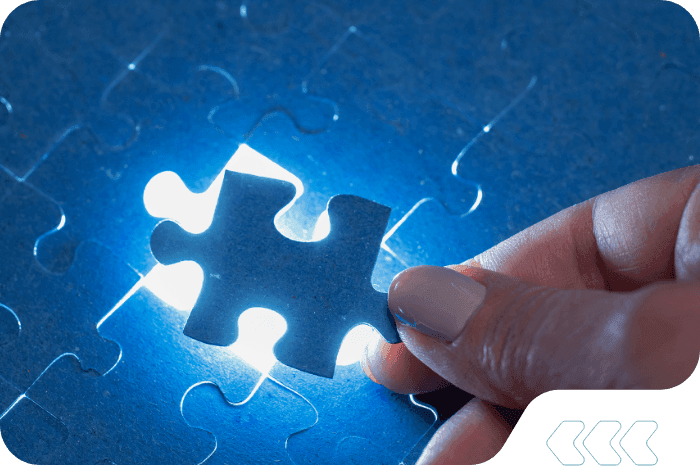
4. Ignoring Legacy Systems and Documentation
Many medical device companies continue to rely on outdated systems for documentation and change management. Legacy systems that are not designed to handle modern compliance requirements can introduce errors, increase audit risks, and slow down remediation efforts. In some cases, inadequate record-keeping may result in an inability to demonstrate compliance to regulatory authorities.
Investing in modern quality management systems (QMS) and electronic documentation tools can significantly improve remediation efficiency. Digital solutions enable better tracking of changes, enhance data integrity, and ensure real-time access to critical compliance information. A proactive approach to upgrading legacy systems strengthens compliance efforts and helps prevent future regulatory challenges.
5. Resource Overextension and Underestimation of Effort
One of the most common early-stage mistakes is underestimating the time, effort, and resources required for successful remediation. Companies often assign remediation tasks on top of existing workloads, leading to burnout, missed deadlines, and poor-quality outcomes. Additionally, unrealistic budgets and timelines can result in rushed efforts that fail to address compliance issues adequately.
To prevent resource overextension, organisations must conduct a realistic assessment of the remediation effort and allocate dedicated personnel to the project. This may involve hiring external consultants, upskilling existing employees, or redistributing workloads to ensure critical tasks receive the attention they require. A well-resourced remediation approach ensures compliance efforts are sustainable and effective.
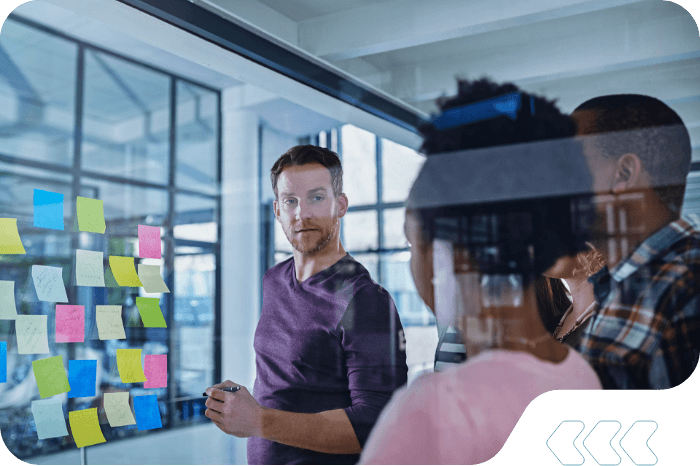
6. Slow or Inadequate Responses to Regulatory Notices
Regulatory agencies such as the FDA issue notices, including Form 483s and warning letters, to highlight compliance deficiencies. Companies that fail to respond promptly and comprehensively increase the risk of further enforcement actions, including product recalls, import bans, or consent decrees.
A robust remediation approach includes a structured response plan for addressing regulatory notices. This involves conducting thorough root cause analyses, implementing corrective and preventive actions (CAPAs), and maintaining clear documentation to demonstrate compliance. Timely and strategic responses help mitigate risks and prevent regulatory escalation.
7. Failing to Engage Experts Early
Remediation is a complex process that requires specialised regulatory knowledge and strategic planning. Companies that attempt to handle remediation internally without seeking expert guidance often struggle with compliance missteps, inefficient processes, and prolonged timelines.
Engaging experienced remediation consultants early in the process can provide valuable insights, streamline efforts, and help avoid costly mistakes. Experts can assist with regulatory interpretations, gap assessments, and strategic planning, ensuring that the remediation approach is comprehensive and aligned with regulatory expectations.
Conclusion
Avoiding early-stage mistakes in medical device remediation is crucial for maintaining compliance, minimising risks, and ensuring product quality. A well-executed remediation approach should include a thorough understanding of regulatory scope, a clear and strategic plan, cross-functional collaboration, modernised documentation systems, adequate resource allocation, timely responses to regulatory notices, and expert guidance.
By proactively addressing these common pitfalls, medical device companies can navigate remediation efficiently, reduce regulatory risks, and position themselves for long-term success.
Trinzo specialises in supporting organisations through complex remediation projects, offering expert-driven solutions to streamline compliance efforts.
SME Insight:
Steve Martin – Quality Centre of Excellence Lead
“I’ve worked on several remediation projects over the course of my career and proper evaluation of the issues, planning, and resourcing the project with professionals possessing the required expertise is essential to a successful outcome. Early engagement with an experienced consulting company like Trinzo will ensure your company can successfully navigate through what can be a difficult process.”
Contact Jim Perry, Director of Client Partnerships, to learn how our tailored approach can help you achieve compliance excellence.